Project Description
Circuit Board Coating Protection
Why do circuit boards need to be protected with coating
The protective coating is used to enhance the performance and reliability of printed circuit board assembly, so that it can be used in harsh environments such as underwater, aerospace and military applications. Manufacturers of electronic consumer products are increasingly using protective coatings as an economical way to improve product reliability.
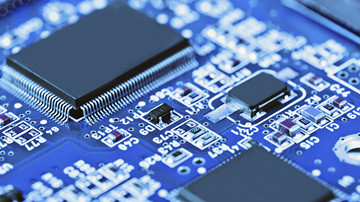
When a printed circuit assembly board without a protective coating is exposed to humid air, a thick film of water molecules will form on its surface, reducing the surface insulation resistance (SIR) of the circuit board. The lower the surface insulation resistance, the worse the transmission performance of electrical signals. The typical consequences are crosstalk, electrical leakage and transmission interruptions, which may lead to permanent signal interruption, that is, short circuit.
The moisture film on the printed circuit board without protective coating also provides favorable conditions for metal growth and corrosion, which will eventually affect the insulation strength and high-frequency signal, dust, dirt and other environments on the assembly board Pollutants continuously absorb moisture, which amplifies its negative effects. Conductive particles such as metal fragments can also cause electrical bridging.
The protective coating is a layer of plastic film wrapped around the printed circuit assembly board. The thickness of this film is 0.005in. It seals dust and environmental contaminants on the outside of the circuit board. Of course, the protective coating may also seal the contaminants not removed during the pre-cleaning process. Therefore, it is very important to clean the surface of the circuit board before applying the protective coating.
The role of the protective coating is as follows:
1) Protect the circuit away from extreme environments and avoid the influence of moisture, fungi, dust and rust;
2) Prevent the circuit board from being damaged during the production, assembly and use process, reduce the mechanical stress on the components and protect it from thermal oscillation;
3) Reduce wear during use;
4) Since the protective coating increases the insulation strength between the conductors, it strengthens the performance of the circuit board and allows greater component density.
How to evenly coat the protective coating on the surface of the circuit board
UAM6000 ultrasonic film spraying equipment combined with new spray and control technology can achieve more uniform, thinner and more controllable film coating. The equipment integrates multiple systems, such as ultrasonic, carrier gas, heating stage, vacuum adsorption and exhaust gas discharge, and can be applied to a full range of ultrasonic nozzles, suitable for small or medium area thin film preparation, and suitable for spray pyrolysis applications. This equipment is widely used in the field of fine coating preparation.
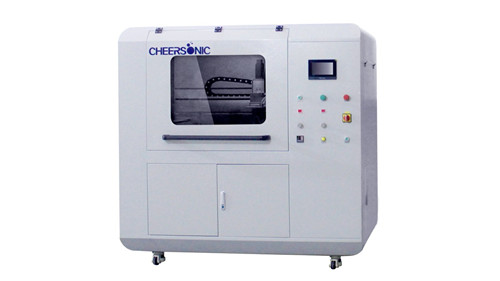
Circuit Board Coating Protection – Film Spraying – Cheersonic